Optimum maintenance and care of tool holding systems on CNC machines!
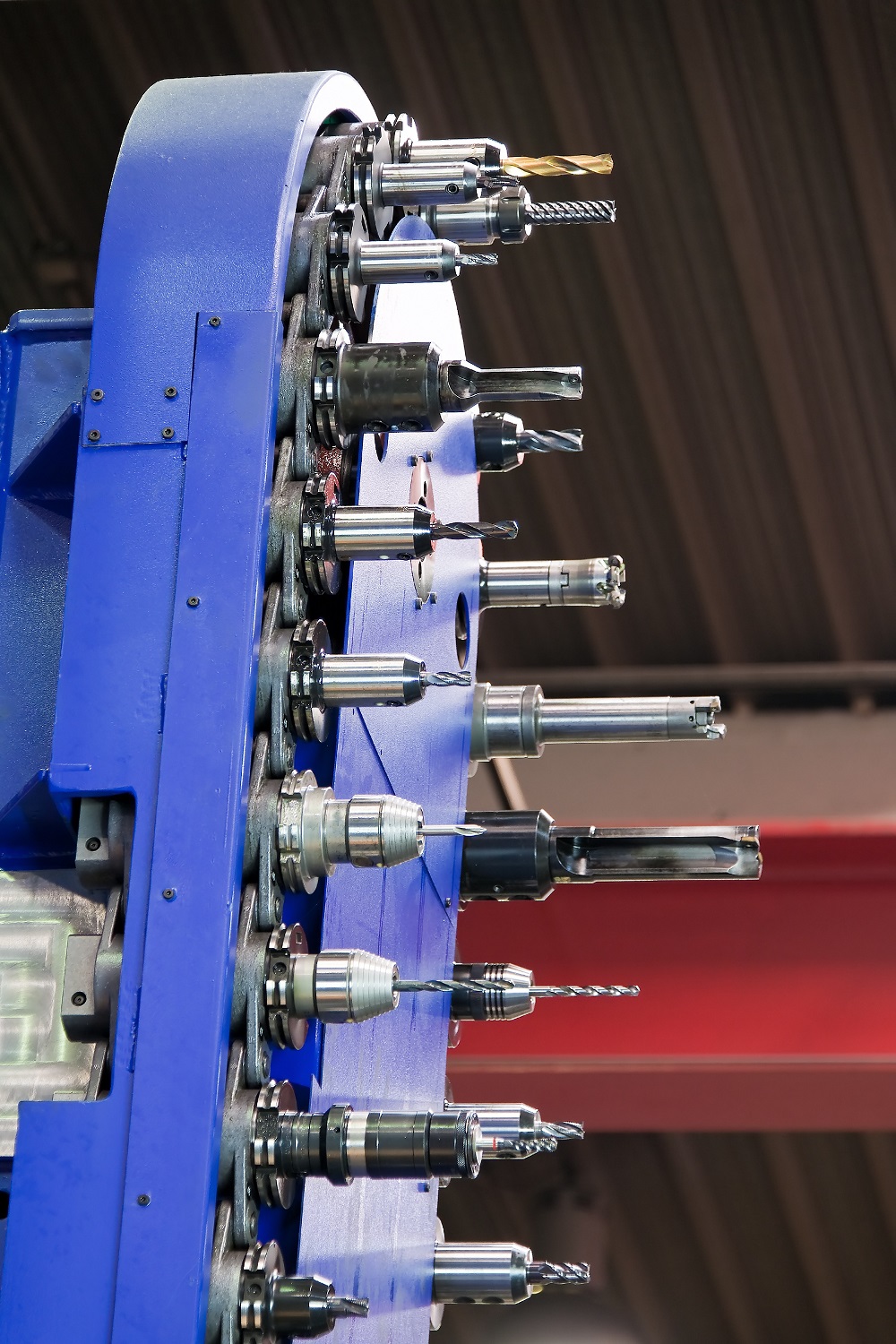
The subject, the facts, the consequence and the solution for the optimal maintenance and care of tool holding systems on CNC machines - in a nutshell!
There are two central criteria that tool holding systems need to fulfil:
• they must enable fast tool changes
In modern CNC machines three types of tool holders are used:
• tool holders with a Morse taper
In order to be able to ensure the above-mentioned criteria of quick tool changing and precision production, it is necessary for the mechanical process to function perfectly, regardless of which tool holding system is used.
Possible sources of malfunction
In addition to mechanical faults due to material wear or the like, gumming of the gripping and clamping devices is usually to be expected. Some of the malfunctions caused by this are described below.
- The tool sticks in the magazine. As a result, the grab is unable to retrieve the tool from the magazine and a malfunction message is generated. The machine stops, the operator has to remove the tool from the magazine by hand and insert it into the tool holder.
- The tool sticks in the spindle. After use, the grab is unable to remove the tool from the tool holder. This results in a malfunction message. The machine stops and the operator has to remove the tool from the spindle by hand.
- The tool is not gripped properly by the grab. In the worst case the tool can fall out of the grab. Either it falls into the machine or into the magazine area. Either way, the operator has to retrieve the tool, check for any damage and insert it by hand.
- The grab inserts the tool asymmetrically into the spindle. Although the grab retrieves the tool, it is not inserted symmetrically into the tool clamp of the spindle due to the deposits sticking to the taper. This leads to size discrepancies in the machining process. Reworking may be necessary or rejects may be produced.
- The tool can't be gripped with the intended force. If the tool taper, the spindle holder - or in the worst case both - are not clean, the grab will not pull the tool into the spindle with the designated force. The result may be a tool that is inserted crookedly or that falls out. The effects have already been described above.
The cause
It may seem paradoxical at first, yet the oil content of the coolant is the cause of the problem. The reason is easy to explain: while the tool is in use it comes into contact with coolant or is exposed to the oily mist of the coolant. After the tool has been used it is replaced by the next one. The first tool is returned to the magazine and waits for its next use. During this time, the coolant residues dry on the surface of the tool. As we know, over time oil gums up and becomes sticky. The surface of the tool becomes sticky and the mechanical mobility in the gripping elements is impaired, as explained above. The tools are no longer gripped or clamped properly.
Incidentally, it makes no difference what kind of tool holding system is involved. The effect of oil resinification is always the same. In any case, a malfunction in the tool changer means that the machine comes to a standstill and production is impaired or lost. The duration of the production disruption varies, of course, from case to case. However, one thing can be said here: the financial impact is enormous whatever happens!
The solution
The solution is relatively simple. Both as a preventive measure in the sense of "predictive maintenance", i.e. the preventive maintenance and care of tool holding systems, and in the acute event of a malfunction, the innotech fluid "HLW100” is particularly well suited. This fluid features innotech tricomplex Technology® and has decisive advantages over maintenance sprays containing oil.
1. It contains a cleaning complex which safely removes deposits and resin from the joints of the clamping device and the tapers of the tools.
2. The effective additives ensure the safe and long-lasting mobility of all the joints, the grab components, the cleanliness of the tool tapers and safe corrosion protection.
3. The substances in the HLW100 fluid are resistant to ageing and don’t gum up.
4. The effect is maintained in spite of spraying by the cooling lubricant.
Put us to the test. We look forward to hearing from you!
There are two central criteria that tool holding systems need to fulfil:
• they must enable fast tool changes
• they must ensure that the workpiece can be manufactured with a high degree of accuracy.
In modern CNC machines three types of tool holders are used:
• tool holders with a Morse taper
• tool holders with a steep taper
• tool holders with a hollow shank taper
In order to be able to ensure the above-mentioned criteria of quick tool changing and precision production, it is necessary for the mechanical process to function perfectly, regardless of which tool holding system is used.
Possible sources of malfunction
In addition to mechanical faults due to material wear or the like, gumming of the gripping and clamping devices is usually to be expected. Some of the malfunctions caused by this are described below.
- The tool sticks in the magazine. As a result, the grab is unable to retrieve the tool from the magazine and a malfunction message is generated. The machine stops, the operator has to remove the tool from the magazine by hand and insert it into the tool holder.
- The tool sticks in the spindle. After use, the grab is unable to remove the tool from the tool holder. This results in a malfunction message. The machine stops and the operator has to remove the tool from the spindle by hand.
- The tool is not gripped properly by the grab. In the worst case the tool can fall out of the grab. Either it falls into the machine or into the magazine area. Either way, the operator has to retrieve the tool, check for any damage and insert it by hand.
- The grab inserts the tool asymmetrically into the spindle. Although the grab retrieves the tool, it is not inserted symmetrically into the tool clamp of the spindle due to the deposits sticking to the taper. This leads to size discrepancies in the machining process. Reworking may be necessary or rejects may be produced.
- The tool can't be gripped with the intended force. If the tool taper, the spindle holder - or in the worst case both - are not clean, the grab will not pull the tool into the spindle with the designated force. The result may be a tool that is inserted crookedly or that falls out. The effects have already been described above.
In all the cases just described, as already mentioned, the cause of the malfunctions could be that the tool taper, the gripping and clamping devices are sticky and gummed up.
The cause
It may seem paradoxical at first, yet the oil content of the coolant is the cause of the problem. The reason is easy to explain: while the tool is in use it comes into contact with coolant or is exposed to the oily mist of the coolant. After the tool has been used it is replaced by the next one. The first tool is returned to the magazine and waits for its next use. During this time, the coolant residues dry on the surface of the tool. As we know, over time oil gums up and becomes sticky. The surface of the tool becomes sticky and the mechanical mobility in the gripping elements is impaired, as explained above. The tools are no longer gripped or clamped properly.
Incidentally, it makes no difference what kind of tool holding system is involved. The effect of oil resinification is always the same. In any case, a malfunction in the tool changer means that the machine comes to a standstill and production is impaired or lost. The duration of the production disruption varies, of course, from case to case. However, one thing can be said here: the financial impact is enormous whatever happens!
The solution
The solution is relatively simple. Both as a preventive measure in the sense of "predictive maintenance", i.e. the preventive maintenance and care of tool holding systems, and in the acute event of a malfunction, the innotech fluid "HLW100” is particularly well suited. This fluid features innotech tricomplex Technology® and has decisive advantages over maintenance sprays containing oil.
1. It contains a cleaning complex which safely removes deposits and resin from the joints of the clamping device and the tapers of the tools.
2. The effective additives ensure the safe and long-lasting mobility of all the joints, the grab components, the cleanliness of the tool tapers and safe corrosion protection.
3. The substances in the HLW100 fluid are resistant to ageing and don’t gum up.
4. The effect is maintained in spite of spraying by the cooling lubricant.
Put us to the test. We look forward to hearing from you!